What is a mechanical process?
In civil engineering, the materials have to undergo a series of manufacturing processes before using them in construction and structural applications. These manufacturing processes form the foundation stone of mechanical processes. Some of the civil engineering materials such as bars, metallic beams, metallic columns, surveying equipment, earthmovers, overhead cranes, structural and construction components, and even cement that is the most fundamental construction component need to undergo different manufacturing processes before they are ready to use. These processes are mechanical.
The process usually begins in the manufacturing industry with materials processing, which involves the selection of raw materials such as sand, silica, steel, plastics, iron, and so on. The materials undergo a systematic chain of manufacturing processes that includes sophisticated machinery and power tools. These tools perform different operations on the materials before the material turns into a finished product.
Here, in this article, a brief outline has been provided about the different manufacturing processes and operations which are carried out in industries to manufacture a product.
Different manufacturing processes
After the preliminary stage of materials processing, the materials are subjected to various mechanical processes and undergo different manufacturing processes. Manufacturing processes are classified into three basic categories. These are outlined below.
Hot forming manufacturing processes
In the hot forming manufacturing process, the component to be manufactured is prepared in the form of a mold. A mold is a cavity prepared in clay, sand, steel, or materials. The mold bears the shape of the end product with added tolerances. Due to the addition of these tolerances, the dimensions of the cavity exceed by a few millimeters. The cavity of the mold is prepared by making use of patterns which are machined pieces of metal.
Raw material in the molten state is added into this cavity, which solidifies and takes the form of the shape of the cavity that is the component to be formed. A furnace is responsible to convert the raw material from its solid state to a liquid state. Solidification initiates dendritic growth. Different metals in a molten state are added to the mold cavity to enhance the strength and other properties of the component. Casting is a popular example of such a manufacturing process.
Other hot forming processes such as hot rolling and forging require the material to be heated above their recrystallization temperature. The material at this stage is subjected to gradually applied loads or impact loads to convert the material to achieve the required shape and dimensions.
Subtracting manufacturing process
This is a kind of manufacturing process which involves the exclusion of materials to produce the required component. This manufacturing process makes use of specialized machines and tools to carve out the component out of the raw materials or workpiece. Workpieces, often in the form of bars having different cross-sectional areas and lengths, serve as input to the machines. To achieve the required dimension and shape, the tool makes contact with the workpiece and via tool or workpiece motion combined with the application of force, removes material in the form of chips due to shearing or shear failure. In this type of manufacturing, there is always a relative motion between the workpiece and the tool. The tool may also move parallelly, perpendicularly, and obliquely about the workpiece. In this manufacturing process, the materials generally used are ductile materials that are worked till their fracture point. Shape operating, milling, and other machining processes are some of the examples of this category.
Additive manufacturing process
Additive manufacturing processes are also known as rapid prototyping processes. It is a new addition to the world of manufacturing and it has been revolutionizing the industry. The additive manufacturing process, unlike the subtractive manufacturing process, does not remove materials, instead, it adds materials layer by layer to form the complete component.
Such a manufacturing process usually uses a computer to design the required component in computer-aided design (CAD) software. The model is converted to standard triangulation language (STL) files. It generates the CAD model made of spline curves and line algorithms into a series of triangles joined together at the nodes, also known as a mesh. The mesh is then executed in a slicing tool and cuts the model into multiple small layers. A computer program then writes specific G-codes regarding each layer. G-code is a machine guiding code that especially guides the tool of the machine to perform specific movements. These codes are then transferred to an additive manufacturing machine, often known as a 3D printer, which manufactures the component layer by layer by melting raw materials in the form of filaments. Different filament materials are polylactic acid (PLA), acrylonitrile butadiene styrene (ABS). Some metallic filaments and nylon filaments are also available.
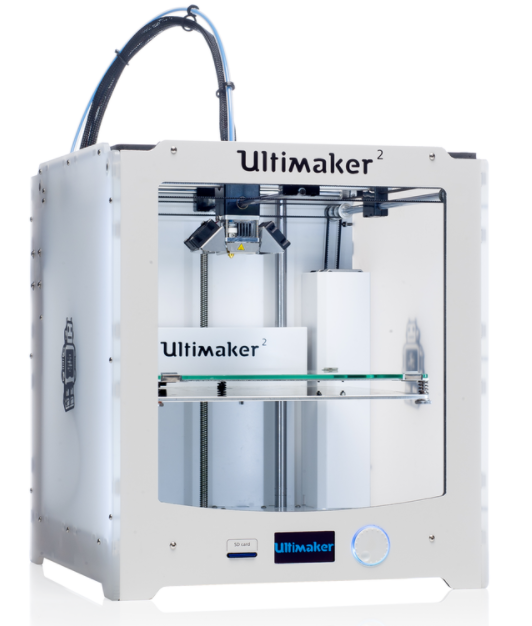
The casting process
Casting is a hot forming process that uses a mold to contain the molten liquid. Sufficient measures and tolerance must be provided to avoid casting defects. Some of the popular casting processes are outlined below.
Mold casting
This casting process allows the use of a single mold to manufacture multiple components. In this casting process, the mold is generally made of sand, clay, binders, and other refractory materials. The mold used has two parts, the cope, and drag. While pouring the metal, both the parts remain joined together. The solidified metal is removed by opening the two mold parts.
Centrifugal casting
This type of casting produces large-sized hollow cylindrical castings that do not require the use of cores. The mold in this casting is in the form of hollow cylinders. The material is poured into the center of a rotating mold. Due to high-speed rotations and centrifugal forces, the material gets deposited at the internal periphery of the mold.
Die casting
The die makes use of pressure to inject the molten material into a per-formed die that has the shape of the component to be produced. The advantage of such casting is that many intricate and complex shapes can be manufactured which cannot be made by simple mold casting.
The welding process
Welding is a metal joining process that performs the job by subjecting the area of metals to be joined to their melting points. This task is done by a welding machine that has a welding torch and an electrode. There are varieties of welding techniques available. Some of them are outlined below.
Arc welding
This welding makes use of a welding electrode and a thing long electrode made of metal with flux coating around its periphery. Welding is powered by a transformer. The electrode is made to touch the metal surface which initiates the flow of electrons. Upon maintaining a gap between the electrode and the material, the flow of electrons is restricted, due to the high voltage and potential applied, the electrons jump, breaking the air barrier and bonds, the energy of bonds is converted to heat energy and it ionizes the gap. The heat from ionization is used in melting and joining.
Friction welding
Friction welding is a popular mechanical process that joins metals by the application of friction. One of the metals is held stationary while the other can undergo both rotational and linear motion. The rotating metal is made to contact the stationary metal which generated heat due to friction. Upon melting by heat, a gentle linear motion is provided that joins the two metals.
Context and Applications
This topic is extensively taught in various undergraduate and postgraduate degree courses of:
- Bachelors in Technology (Mechanical engineering, Civil engineering, Manufacturing engineering)
- Master in Technology (Mechanical engineering, Civil engineering, Manufacturing engineering)
- Masters in Science in Production technology
Practice Problems
Q 1. What is the preliminary stage before a manufacturing process?
a. Materials processing or selection
b. Materials operation
c. Machining process
d. None of these
Answer: Option a
Explanation: The preliminary stage before a manufacturing process is materials processing or selection.
Q 2. Which of the following is a hot forming manufacturing process?
a. Welding
b. Casting
c. Hot rolling
d. Both b and c
Answer: Option d
Explanation: Hot rolling and casting both are examples of hot forming processes.
Q 3. What is the other name of rapid prototyping?
a. Slicing
b. 3D printing
c. Subtractive manufacturing
d. Both a and b
Answer: Option b
Explanation: The other name of rapid prototyping is 3D printing.
Q 4. Which of the following manufacturing processes subjects the material to fracture?
a. Subtractive manufacturing
b. Additive manufacturing
c. Hot forming manufacturing
d. All of these
Answer: Option a
Explanation: In subtractive manufacturing, the material or the workpiece is subjected to its failure points.
Q 5. What are the characteristics of a fusion welding process?
a. It uses the heat of ionization.
b. It has linear motion only.
c. It has both linear motion and rotational motion.
d. it has rotational motion only.
Answer: Option c
Explanation: In the fusion welding process one of the material possess both linear and rotational motion.
Want more help with your civil engineering homework?
*Response times may vary by subject and question complexity. Median response time is 34 minutes for paid subscribers and may be longer for promotional offers.
Search. Solve. Succeed!
Study smarter access to millions of step-by step textbook solutions, our Q&A library, and AI powered Math Solver. Plus, you get 30 questions to ask an expert each month.
Environmental engineering
Solid waste disposal methods
Mechanical processes
Mechanical Processes Homework Questions from Fellow Students
Browse our recently answered Mechanical Processes homework questions.
Search. Solve. Succeed!
Study smarter access to millions of step-by step textbook solutions, our Q&A library, and AI powered Math Solver. Plus, you get 30 questions to ask an expert each month.