What is meant by materials management?
Materials form the basic ingredient or the raw supplies before the final product. Materials cover the inventory storage in typical warehousing. All manufacturing processes and production processes require different materials.
Supply chain management forms the base of materials management, which involves different levels of planning and procedures to execute supply chains successfully to meet the material requirements of a company. Some of the key procedures involve material procurement, control and flow of materials, storage of materials, inventory management, and so on.
The materials management process adds value to a business. It also includes the procurement of machinery and other equipment, which ensures dedicated production schedules and product delivery on time. There are different roles played by the materials management teams such as inventory analysts, inventory control managers, material managers, material planners, and expediters.
Material types
There are two types of materials handled by the materials management system, direct type, and indirect type materials. They are outlined below.
Direct materials
Direct materials are the primary ingredients of the final product being sold to the consumers. They generally decide the overall cost and market value of the product. Proper materials management planning ensures the availability of these materials for the core manufacturing process. Poor management system leads to failure and also directs the company towards losses. Plastics, cement, beams, bars, steel, metallic and non-metallic materials, bolts, nuts, screws, and so on, are some of the examples of direct materials.
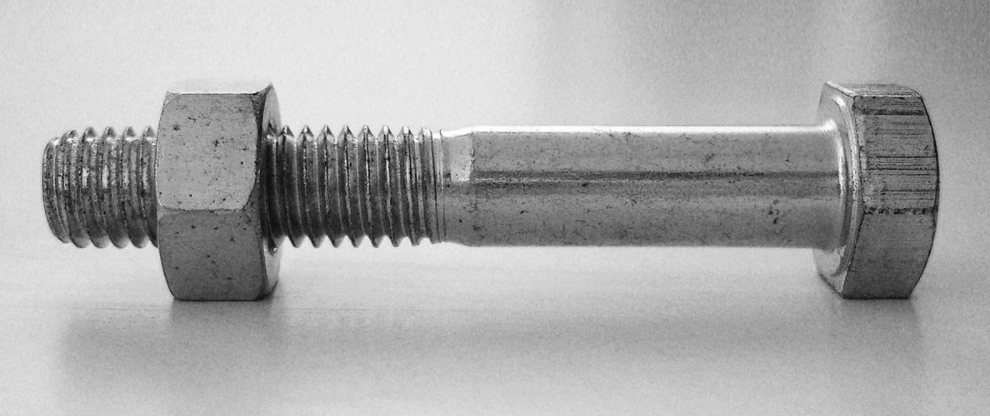
Indirect materials
Indirect materials are those materials that do not form the primary part of the end product but form a part of the manufacturing process of the product. Their absence will not cause direct harm to the company and can be compensated by alternative means. Equipment, lubricants, oils, power tools, spare parts, all these are some of the examples of indirect materials.
Techniques of materials management
Planning forms a vital step towards successful materials management. Inadequate or poor planning might pose a threat to the organization or business. As a modern tool, there are various material management tools, some of which are discussed below.
Material requirements planning (MRP)
MRP is a planning and decision-making tool used by manufacturing companies. This planning procedure makes use of the forecasting technique as its most defensive tool. MRP makes a comparison between the current inventory levels and the production capacity of the company. It decides the requirement of manufacturing goods. This system is fully computerized.
MRP functions through some basic features, they are:
- Master production schedule: It includes the planning, orders, and forecasts.
- Bill of materials (BOM): This includes the details of all the components and construction materials required to make the product.
- Inventory status file: Involves inventory details in the documentation, including gross and net requirements.
MRP system involves three steps, they are:
- Exploding: This step depends on the BOM. The BOM reflects the requirement of several materials to manufacture a single product.
- Netting: This step provides the material management system with information regarding the materials involved in manufacturing. This is evaluated by calculating the difference between the available inventory in the factory and the gross inventory needed.
- Offsetting: This step directs the time period about starting the manufacturing process, based on lead time calculations, by the project management team.
Enterprise resource planning (ERP)
Unlike MRP, which focuses on materials planning, the ERP functions as a modified version of the MRP. ERP involves all the activities, that involve the management of enterprises. In this category of material management, the material manager is provided with specific tools that help in efficient material management and planning. ERP was established after the MRP, when various organizations realized that, management of offices and enterprises are equally important like material management. ERP functions with a centralized database system, that thrives in the simplification of labor with the increase in the workflow.
Inventory management
An inventory management system involves a set of methodologies that tracks the flow of goods throughout the whole process. The system tells about the number of materials, which are essential commodities of the final product. The inventory management system also directs a company on keeping excess stock in case of extensive lead times and raw material shortages.
Functions of material management
There are four functions of the materials management system, which are outlined below.
Purchasing
The basic and prime function of material management is purchasing. Right and efficient purchasing ensures production continuity, material procurement at the best production value, and increase profits with added product promises.
Inventory management
This means managing the stock of raw materials including both essential and non-essential materials at the optimum level to ensure smooth production flow.
Store management
Proper warehousing involves inspections, proper receipts, safe storage of materials, and proper documentation. This step in materials management ensures the loss of materials and production bottlenecks.
Disposal of scrap materials
This is one of the important steps in the material management system. Obsolete materials get accumulated over time with an ongoing manufacturing process. Disposal of such materials ensures good production, with the use of only relevant materials that are meant for that particular product.
Context and Applications
This topic is extensively taught in various undergraduate and postgraduate degree courses of
- Bachelors of Technology in Mechanical Engineering
- Bachelors of Technology in Civil Engineering
- Masters of Technology in Mechanical Engineering
- Masters of Technology in Civil Engineering
Practice Problems
1. Which of the following forms a direct material of a construction firm?
- Cement
- Concrete mixture
- Reinforcement bars
- Both a and c
Answer: Option d
Explanation: Cement and reinforcement bars form the important direct materials of a construction firm.
2. Which of the following is an indirect material of the automobile industry?
- Steel
- Fiber materials
- Lubricating oil for press machines
- Fasteners
Answer: Option c
Explanation: Lubricating oil for press machines is an example of indirect material of the automobile industry.
3. Which of the following is the function of material management?
- Purchasing
- Inventory management
- Forecasting
- Both a and b
Answer: Option d
Explanation: Purchasing and inventory management forms are the two basic functions of material management.
4. What is the full form of MRP?
- Material requirement planning
- Materials requirement planning
- Materials requirements planning
- Material requirements planning
Answer: Option d
Explanation: The full form of MRP is material requirements planning.
5. What is the full form of BOM?
- Bill of material
- Bill of materials
- Bills of material
- None of these
Answer: Option b
Explanation: The full form of BOM is a Bill of materials.
Want more help with your civil engineering homework?
*Response times may vary by subject and question complexity. Median response time is 34 minutes for paid subscribers and may be longer for promotional offers.
Search. Solve. Succeed!
Study smarter access to millions of step-by step textbook solutions, our Q&A library, and AI powered Math Solver. Plus, you get 30 questions to ask an expert each month.
Management of Materials Homework Questions from Fellow Students
Browse our recently answered Management of Materials homework questions.
Search. Solve. Succeed!
Study smarter access to millions of step-by step textbook solutions, our Q&A library, and AI powered Math Solver. Plus, you get 30 questions to ask an expert each month.