What is Corrosion?
Corrosion may be defined as the method in which metals are attacked on their exteriors by gases existing in the atmosphere, converting them to their oxides, nitrides, sulfides, etc.
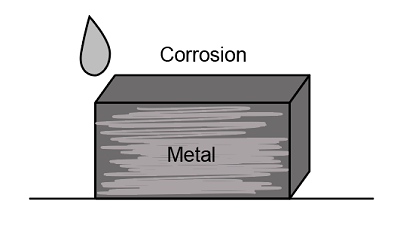
Corrosion is a redox reaction that includes both oxidation and reduction in one single reaction. In this reaction, the metal gets oxidized, and the atmospheric gases get reduced. It involves the oxidation of metal, which acts as an anode, and the reduction of atmospheric gases, which acts as a cathode. The anode is considered as a metal that gets corroded, and the cathode is a dissimilar metal that has lesser tendencies to get corroded. Magnesium, aluminum, and lithium are some materials that get corroded easily, and carbon/graphite, platinum, gold, silver, titanium are some materials that do not get corroded easily.
The image below shows the corrosion in iron, commonly known as rust.
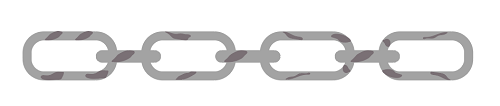
What are the types of corrosion?
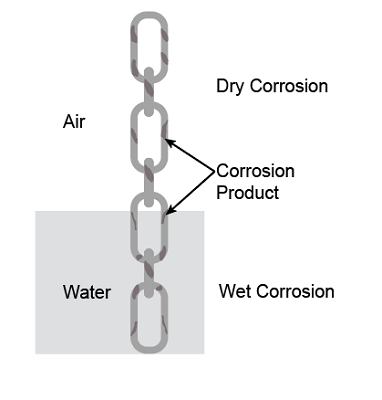
There are the following two types of corrosion:
- Dry corrosion
- Wet corrosion
Dry corrosion
Dry corrosion is a method that does not need any electrolyte or medium for its appearance.
Dry corrosion can be further categorized into three types:
- Oxidative corrosion
- Corrosion by other gases
- Liquid metal corrosion
Wet corrosion
Wet corrosion is described as corrosion that needs an electrolyte or a medium for its appearance. Example: Oxidation of iron is recognized as rusting of iron. Here, water serves as the electrolyte and facilitates the transfer of electrons from anode to cathode. As a result, the rate of corrosion is much quicker in wet corrosion as compared to dry corrosion. Galvanic corrosion is also a type of wet corrosion. Galvanic corrosion happens when two different metallic materials are electrically joined in corroding conditions. By adding some inhibitors, galvanic corrosion can be avoided.
What is corrosion control?
Corrosion control may be defined as protecting the surface of the metal so the corrosion reaction does not take place at the surface of the metal.
There are several methods to control corrosion:
- Metallic coating
- Corrosion inhibitors
- Organic coatings or protective coatings
- Using pure metal
- Using alloys
- Inorganic coating
- By modifying the environment
- Cathodic protection
- Proper designing
Metallic coating
The metallic coating gives a layer on the metal surface that changes the surface properties of the workpiece to those of the metal being applied. It can be further classified into the five subcategories:
- Electroplating
- Metal cladding
- Hot dipping
- Cementation
- Metal spraying
Electroplating
It is the most commonly used corrosion protection method. It can be defined as the corrosion protection process by which a coating material is deposited on the base metal surface by passing a direct current through an electrolyte solution. It is usually employed for decorative purposes or to protect a metal surface from corrosion.
Metal cladding
It can be defined as the corrosion protection method in which the base metal is to be preserved, and the coating metal is sandwiched by pressing with rollers following the action of pressure and heat.
Hot dipping
In this kind of corrosion protection method, the base metal to be coated is immersed in a bath of the molten coating metal. It is considered an economic process, and the main advantage of this method is that it provides a thick coating for loner corrosion protection.
Cementation
In this kind of corrosion protection method, a smooth surface coating is achieved by heating the base metal in the power of the coating material.
Metal spraying
The metal spraying corrosion protection method can be described as the process in which the coating metal in the molten phase is sprinkled on a base metal surface by means of a spraying gun.
Corrosion inhibitors
Corrosion inhibitors may be defined as the substances superimposed in small amounts on the surface of the metal. It decreases the corrosion rate of the metal when exposed to an unfavorable environment. Corrosion inhibitors are extensively used in industries to minimize metal loss and acid consumption. Corrosion inhibitors are of the following two types:
- Anodic inhibitors
- Cathodic inhibitors
Anodic inhibitors
Anodic inhibitors are also known as passivators. They help in forming an oxide film on the surface of the metal, causing corrosion resistance. As the inhibitor concentration increases, the protective layer will be established fully, leading to a decrease in the corrosion rates. Examples of Anodic inhibitors are Nitrite, Molybdate, and Orthophosphate.
Cathodic inhibitors
Cathodic inhibitors can reduce the rate of reaction happening at the cathode or increase the impedance on the cathode, reducing the corrosion taking place at the cathode. The extent of inhibition or effect depends on factors such as flow regime, water quantity, and fluid composition. Examples of cathodic inhibitors are calcium carbonates and polyphosphates.
Organic coatings or protective coatings
The organic coatings are applied on metallic surfaces to protect them from corrosion and impact a decorative value. It can be further classified into the four subcategories:
- Paints
- Enamel
- Varnishes
- Lacquers
Paints
These are mechanical dispersion mixtures of finely divided solids called pigments in a fluid medium.
Enamel
It is a dispersion of pigments in varnish.
Varnishes
It is a colloidal solution of synthetic and natural gum in solvents like oil and spirit.
Lacquers
It is a colloidal dispersion of a solution of cellulose derivatives like cellulose nitrates, resins, and plasticizers in a solvent.
Using pure metal
A pure metal consists of a single element, which indicates that it is a metal having an individual kind of atom in it. Examples of pure metals are copper, iron, zinc, etc. Pure metals are homogenous and have corrosion resistance. Greater the purity of metal more will be the corrosion resistance.
Using alloys
An alloy is a composite of two or more pure elements. Pure metals sometimes lack certain needed characteristics. To generate these properties, a number of these pure metals are joined together. The homogenous alloys are more corrosion resistant than pure metals.
Inorganic coating
The inorganic coatings are created by chemical or electrochemical reactions at the surface of the metal. This coating gives protection to the base metal from corrosion. Some inorganic coatings are chrome, oxides, phosphates, etc.
By modifying the environment
Reducing the temperature decreases the corrosion. The elimination of moisture by the addition of adsorbents like alumina or silica gel leads to a reduction in corrosion. The acidic corroding atmosphere can be neutralized by the supplement of ammonia, lime, or sodium hydroxide. An improvement in humidity causes an increase in the rate of corrosion as water improves the transfer of electrons from anode to cathode. So by reducing the humidity, corrosion can be avoided.
Cathodic protection
The cathodic protection or electrochemical protection develops the supply of electrons to metal by forcing the metal to behave as a cathode, and as a result, the metal is not corroded. Cathodic protection can be achieved in two ways:
Sacrificial anodic protection
In this corrosion protection method, the metallic equipment to be protected is connected to a more anodic metal, so the metallic equipment acts as a cathode, and the anodic metal works as an anode. As a result, corrosion takes place at the anode, and cathodic metallic equipment is saved from the corrosion.
Impressed current cathodic protection
This process consists of connecting the material to be protected to the negative terminal of the dc source. The positive terminal of the dc source is connected to an insoluble anode like graphite, carbon, and scrap iron. The current supplied is in the direction opposite to the corrosion current. Thus, the metal to be protected acts as the cathode and gets protected.
Proper designing
The proper design of the equipment represents a significant role in preventing corrosion. Proper designing can slow down or even avoid corrosion. It avoids the contact of dissimilar metals in the presence of a corroding environment.
Common Mistakes
Students get confused between electrolysis and electroplating. Electrolysis is the method of utilizing a primary electrical current to stimulate a non-spontaneous chemical reaction, while electroplating is the method of plating one metal on another metal utilizing electrical energy.
Students get confused between dry and wet corrosion. The dry corrosion happens in the deficiency of moisture, while the wet corrosion happens in the presence of conducting medium.
Context and Applications
The topic of corrosion control methods is very much significant in the several professional exams and courses for undergraduate, diploma level, graduate, and postgraduate. For example:
- Bachelor of Technology in Mechanical Engineering
- Master of Technology in Mechanical Engineering
- Bachelor of Science in Chemistry
- Master of Science in Chemistry
Related Concepts
- Corrosion metallurgy
- Electrochemistry
- Electrolysis of water
- Galvanization
- Lead storage battery
Practice Problems
Q1: Which of these elements can be used to protect the iron from rusting by using galvanization?
(a) Sn
(b) Cu
(c) Pb
(d) Zn
Correct option: (d)
Q2: Among the four options, which of the following doesn’t cause rust on iron?
(a) Vacuum
(b) Moisture
(c) SO2
(d) CO2
Correct option: (a)
Q3: Which of the following is not a process of protection from corrosion?
(a) Anti-rust solutions
(b) Heating
(c) Galvanization
(d) Cathodic protection
Correct option: (b)
Q4: Which of the following is not required for rusting to occur?
(a) Oxygen
(b) Light
(c) Metal
(d) Moisture
Correct option: (b)
Q5: Which of the following metal does not corrode?
(a) Magnesium
(b) Zinc
(c) Copper
(d) Iron
Correct option: (c)
Want more help with your mechanical engineering homework?
*Response times may vary by subject and question complexity. Median response time is 34 minutes for paid subscribers and may be longer for promotional offers.
Search. Solve. Succeed!
Study smarter access to millions of step-by step textbook solutions, our Q&A library, and AI powered Math Solver. Plus, you get 30 questions to ask an expert each month.
Materials Science and Engineering
Corrosion
Corrosion Control Methods
Corrosion control methods Homework Questions from Fellow Students
Browse our recently answered Corrosion control methods homework questions.
Search. Solve. Succeed!
Study smarter access to millions of step-by step textbook solutions, our Q&A library, and AI powered Math Solver. Plus, you get 30 questions to ask an expert each month.