What is Aggregate Planning?
On the basis of the demand forecast, an organization can complete its business plans. When the business plans are complete, an organization can work backward from the completed total sales to the raw materials needed. Thus, annual and quarterly plans are divided into labor, raw material, working capital, and other demands for a medium-term period (6 months to 18 months). This process of evaluating moderate production requirements is known as aggregate planning.
The amount of outsourcing, subcontracting of items, labor overtime, statistics of offered jobs and fired employees in each period, and the level of inventory to be held in the warehouse and backlogged for each period are all decided. Each of these activities is carried out in accordance with the company's ethics, policies, and long-term commitment to society, community, and country of operation.
The planning consists of many factors such as,
- Human resources
- Raw material
- Financial planning
- Operations
- Engineering
- Marketing and distribution
Importance of Aggregate Planning
Aggregate planning is essential to achieving the organization's long-term goals. Aggregate planning aids in the following areas:
- Obtaining financial objectives by lowering overall variable costs and improving the end result
- Consumption of the available production facility to the greatest extent possible
- Focus on providing consumer satisfaction by matching demand and reducing client's wait time.
- Start reducing your inventory stocking expenditure.
- Capable of meeting scheduling objectives while creating a happy and satisfied workforce
Certain Pre-Requisite Inputs are Unavoidable in Aggregate Planning
They are as follows:
- Information on the available resources and facilities.
- Demand forecast for the time period for which planning is required.
- The cost of various options and resources. This requires the inventory costs, the cost of ordering, and the cost of production via various production alternatives such as subcontracting, backorders, and overtime.
- Organizational policies governing the use of the aforementioned alternatives
Management and Planning Strategies
Aggregate planning assists in achieving a balance between the organization's operational goals, financial goals, and overall strategic goals. It acts as a platform for capacity and demand planning. When demand does not match capacity, an organization can try to balance this through pricing, promotion, order management, and new demand creation
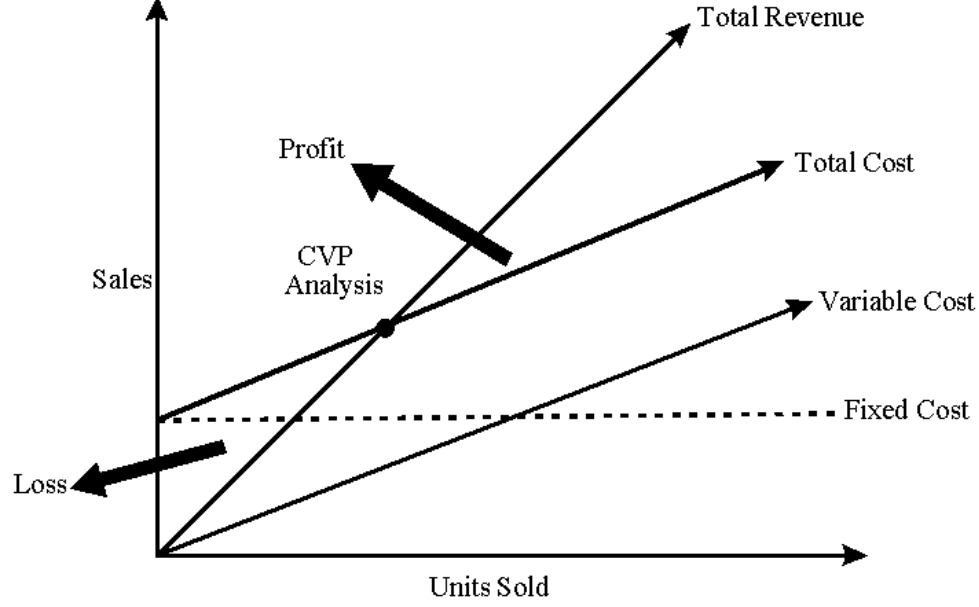
Amongst these overall planning strategies are:
- Level Strategy-This category of aggregate planning is concerned with making goods in similar quantities over an equal time period. This is done to deal with a surge in market demand by filling back orders or sending excess products to inventory.
The level strategy is a traditional aggregate planning method that continues to maintain a consistent rate of production as well as workforce level by maintaining consistent human resources and production in the organization.
It is best suited where inventory carrying costs are low and is mostly used by manufacturing companies. The benefits of using a level strategy include a well-trained workforce with fewer changes, experienced workers, and a low rate of absenteeism and employee turnover.
One significant disadvantage of the level strategy is the accumulation of inventory costs during the lean period when demand is low.
2. Chase strategy-The chase strategy of aggregate planning focuses on inventory reduction. It adjusts to changes in demand by changing either the real level of output or the workforce size.
It is regarded as less rigid than a level strategy because it allows for certain deviation from the conventional approach. By receiving goods only when they are needed, this methodology helps to reduce waste. Employees are frequently stressed as a result.
This strategy is widely used in a variety of industries, including hospitals, hospitality businesses, and educational institutions such as schools. The benefit of the chase strategy is its high flexibility to meet fluctuations in demand, while the disadvantages include high costs associated with hiring and training the workforce.
3. Hybrid strategy-The Hybrid strategy, as the name suggests, combines both level and chase strategies to achieve a better outcome. It strikes a proper balance between stock levels, recruitment, termination, and production rate. Organizations use a hybrid strategy of aggregate planning to stockpile inventory ahead of rising demand. Backorders are used to compensate for high peak periods.
It is effectively able to cover short-term peaks by hiring temporary workers or subcontracting production. Hiring, laying off, and reassigning employees is a regular part of the hybrid strategy.
Problems related to Aggregate Planning
- Smoothing-Smoothing costs are those incurred as a result of shifting production and workforce levels from one-time frame to the next.
- Bottleneck Problems-It is the system's incapacity to pay attention to sudden shifts in demand as a result of capacity constraints.
- Planning Horizon-The number of forecasted periods for demand, and thus the number of forecasted periods for workforce and inventory levels, must be predefined.
Mathematical Approaches to Aggregate Planning
SIMULATION
For aggregate planning, a variety of simulation models can be used. By creating an aggregate plan within the context of a simulation model, it is possible to test it under a number of situations in order to find appropriate plans for consideration. These models can also be integrated into a decision support system to aid in the research and implementation of alternative control policies. By employing various quantitative measures of productivity, customer service, and flexibility, these models can incorporate the multiple conflicting objectives inherent in manufacturing strategy.
The advantages associated with aggregate planning include:
- It enables the organization to deal with production facilities in a more effective manner. If a manufacturing plant has an excess of finished goods, it is not appropriate for it. The likelihood of product damage before reaching the final destination is greater, resulting in the loss. Furthermore, additional inventory costs add to the company's expenses. The only solution to decrease these costs is to implement an effective aggregate planning process.
- The process aids in the implementation of an appropriate strategic plan as well as relationships with distributors and suppliers. It also aids in the development of precise market research.
- Inventory optimization is aided by planning. Holding an excessive amount of inventory will result in additional costs for a manufacturing company. It also necessitates more storage space to keep it effectively because the likelihood of damage increases if the storage space is inadequate. The organization will also need to spend more resources, labor, and equipment to manage and move the inventory. The system produces an accurate estimate of the anticipated inventory that will be able to meet future demands.
The steps involved in creating an aggregate plan:
Step 1 Determine the aggregate plan that best fits your company's goals: level, chase, or hybrid.
Step 2 Evaluate the aggregate production rate based on the aggregate plan.
- When using the level plan with inventories and backorders, the aggregate production rate is set to match the average demand. Furthermore, if no backorders are permitted, the workforce size is initially adjusted to ensure that all demand is met on time.
- Calculate how much generation capacity you need each period if you use the chase aggregate plan. Determine how many units will be generated on a regular and overtime basis, as well as how many will be subcontracted.
Step 3 Determine the workforce size.
- Determine the number of workers required to obtain the necessary average production rate if you use the level aggregate plan.
- If your capacity keeps changing with hires and firings each period, quantify how many employees you need each period and make the necessary changes to your workforce.
- Calculate how much of a particular option you need each period if you change capacity through a variety of options.
Step 4 Put the overall strategy to the test.
- Approximate your inventory levels (excesses and shortages), any shortages you face, the expected number of employees hired and fired, and when you will require overtime using the production rate and initial workforce size.
- Estimate the exact cost of your plan.
Step 5 Evaluate the plan's cost-effectiveness.
Common Mistakes
- Inadequate documentation of records
- Complexity while evaluating metrics. They are unable to ask the appropriate questions due to the complexity.
- The most significant issue we see is that the executive leadership team does not own the Sales and Operations Planning process.
Context & Applications
- We are obtaining financial objectives by lowering overall variable costs and improving the bottom line.
- Utilization of the available production facility to the greatest extent possible.
- Provide customer satisfaction by matching demand and lowering customer wait time.
- Reduce your inventory stocking investment.
Related Concepts
- Supply Chain Management
- Demand & Forecast
- Business Management
Want more help with your operations management homework?
*Response times may vary by subject and question complexity. Median response time is 34 minutes for paid subscribers and may be longer for promotional offers.
Search. Solve. Succeed!
Study smarter access to millions of step-by step textbook solutions, our Q&A library, and AI powered Math Solver. Plus, you get 30 questions to ask an expert each month.
Aggregate Planning Strategies Homework Questions from Fellow Students
Browse our recently answered Aggregate Planning Strategies homework questions.
Search. Solve. Succeed!
Study smarter access to millions of step-by step textbook solutions, our Q&A library, and AI powered Math Solver. Plus, you get 30 questions to ask an expert each month.